Duży nacisk na to, by ładowanie trwało maksymalnie krótko kładą np. inżynierowie Audi. Kierowcy w pełni elektrycznych modeli tego producenta mogą korzystać z szybkiego ładowania, ponieważ przez większą część procesu dostępna jest moc ładowania nawet 150 kW, bowiem system zaawansowanego zarządzania termicznego litowo-jonową baterią daje możliwość ładowania z dużą prędkością i mocą.
Większość procesów ładowania samochodu elektrycznego odbywa się zazwyczaj w domu lub w pracy. Czynnik czasu na ogół nie odgrywa tam istotnej roli. W przeciwieństwie do tego, podczas podróży na duże odległości liczy się każda minuta, a szybkie ładowanie jest tu wręcz niezbędne.
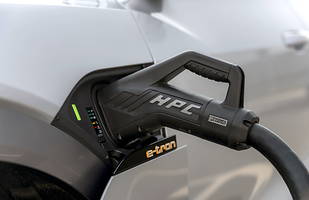
Gniazdo ładowania Audi
W takiej sytuacji samochód powinien być gotowy do kolejnego etapu podróży po maksymalnie krótkiej przerwie. Wielu klientów, aby ocenić charakterystykę samochodu elektrycznego, zwraca przede wszystkim uwagę na maksymalną moc ładowania. Ale wartość ta ma ograniczone zastosowanie, gdy przychodzi do podłączenia samochodu do terminala na stacji szybkiego ładowania. By proces ten trwał jak najkrócej, zasadniczego znaczenia nabiera wtedy szybkość ładowania (kWh / minuta ładowania). Innymi słowy, wysoka wydajność ładowania musi być dostępna wtedy przez jak najdłuższy okres czasu.
Szybkość ładowania ma większe znaczenie niż czysta pojemnośćDzięki wysokiej mocy ładowania, Audi e-tron zajmuje czołowe wśród konkurencji miejsce – nawet gdy na rynku są inne modele o nominalnie wyższej wydajności. Różnica tkwi w szczegółach: zdolność szybkiego ładowania HPC (High Power Charging) na terminalu ładującym, która ma zapewnić możliwie najwyższą moc wyjściową, może być tu warunkiem niezbędnym, ale niekoniecznie kluczowym.
Niemniej ważne jest wysokie zużycie prądu przez dużą część procesu ładowania baterii. Jeśli samochód ładuje się z maksymalną wydajnością przez stosunkowo krótki czas i musi wcześniej obniżyć moc, jednocześnie zmniejszana jest również prędkość ładowania - tzn. bateria jest ładowana z maksymalną mocą przez określoną jednostkę czasu. Zatem dzięki idealnej krzywej ładowania z maksymalną mocą dostępną przez długi czas, czas ładowania jest bardziej istotnym kryterium pod względem wydajności, i ostatecznie gwarantuje krótki postój przy terminalu ładującym. Od tego, ile „zasięgu” można doładować średnio w określonym czasie, na przykład w ciągu dziesięciu minut, zależy również średnie zużycie energii.
Różnica tkwi w krzywej ładowania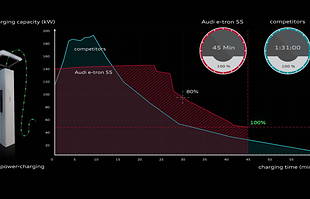
Krzywa ładowania określa jak szybko naładujemy auto
W Audi e-tron 55 krzywa terminala HPC o mocy wyjściowej 150 kW wyróżnia się wysokim poziomem dzięki swej ciągłości. W idealnych warunkach samochód ładuje się do poziomu od 5% do 70% na progu maksymalnej mocy wyjściowej, zanim system zarządzania funkcjonowaniem baterii zmniejszy prąd. To właśnie jest kluczowa różnica w porównaniu z innymi koncepcjami, które zwykle osiągają pełną moc wyjściową tylko przez krótki czas - w szczytowym momencie ładowania - i znacznie obniżają swoją moc przed osiągnięciem progu 70% naładowania.
Koncepcja Audi daje przewagę w codziennym użytkowaniu: jeśli kierowca chce pokonać dystans około 110 kilometrów, na stacji ładowania spędzi niecałe 10 minut. Audi e-tron 55 osiąga poziom 80% naładowania po około 30 minutach. Mimo, że z przyczyn technicznych dużo więcej czasu zajmuje naładowanie pozostałych 20 procent akumulatora litowo-jonowego, pełne naładowanie (od 5% do 100%) na terminalu HPC to około 45 minut.
Zarządzenie temperaturą kluczemLitowo-jonowa bateria Audi e-tron 55 ma pojemność brutto 95 kWh (86,5 kWh netto) i została zaprojektowana z myślą o długim cyklu życia. Zaawansowany system zarządzania termicznego stanowi tu podstawę dobrze zbalansowanej wydajności i trwałości. Chłodzenie cieczą powoduje, że temperatura akumulatora utrzymuje się w optymalnym zakresie od 25 do 35 stopni Celsjusza, nawet przy niesprzyjających warunkach lub w niskich temperaturach otoczenia.
W czterech obwodach (w sumie 40 metrów przewodów) krążą 22 litry płynu chłodzącego. Podczas ładowania prądem stałym o mocy 150 kW, zimny płyn chłodzący odbiera ciepło powstałe w wyniku wewnętrznego oporu elektrycznego akumulatora. Rdzeń układu chłodzenia składa się z wytłaczanych profili, które zostały przymocowane do układu akumulatorów od dołu. Nowo opracowany, przewodzący ciepło klej łączy układ chłodzenia z obudową akumulatora.
Specjalny wypełniacz szczelin – żel przewodzący ciepło - umożliwia pełny kontakt między obudową a umieszczonymi w niej modułami ogniw. Żel wypełnia wszystkie szczeliny między elementami i równomiernie, poprzez obudowę akumulatora, przenosi ciepło odpadowe wytwarzane przez ogniwa wprost do płynu chłodzącego. Oddzielenie elementów w przestrzeni zwiększa bezpieczeństwo systemu. Dodatkowym pozytywnym efektem tego skomplikowanego projektu jest wysoka odporność podczas wypadku.